如何通过金相检测判断SIM卡座弹片疲劳度?
- 分享
- 发布时间
- 2025/5/14
概要
在电子连接器领域,SIM卡座弹片的疲劳度直接影响产品的使用寿命和可靠性。作为长期承受插拔应力的关键部件,弹片在反复形变中易发生微观结构变化,最终导致断裂或接触失效。摩凯电子通过金相检测技术,结合材料科学与工程经验,形成了一套高效判断弹片疲劳度的分析方法。以下是具体实践方案:
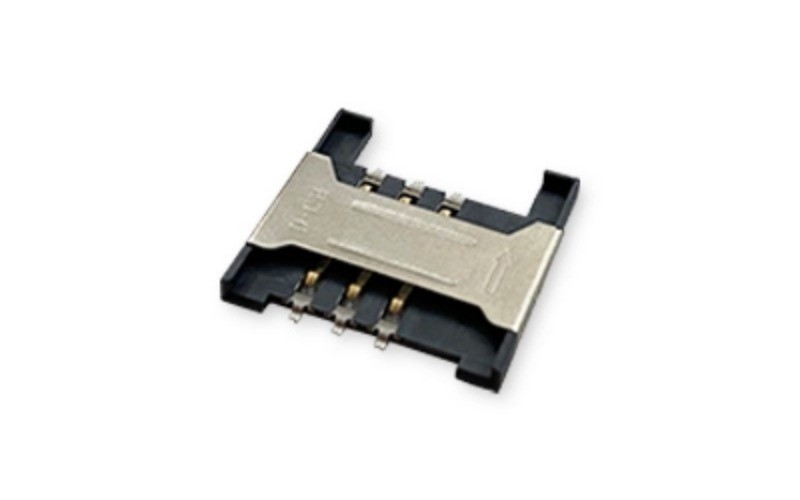
一、弹片疲劳的微观机制与金相检测关联性
一、弹片疲劳的微观机制与金相检测关联性
弹片材料(如磷青铜、铍铜等)的疲劳失效通常始于微观缺陷(如晶界裂纹、夹杂物)或组织退化(如晶粒粗化、相变)。金相检测通过观察以下关键指标判断疲劳程度:
裂纹萌生与扩展:疲劳初期,材料内部或表面会形成微裂纹,通过金相显微镜可捕捉裂纹的分布、长度及走向(图1)。例如,在500倍放大下,若发现晶界处存在沿晶裂纹或穿晶裂纹,表明材料已进入疲劳中期阶段。
晶粒形态变化:反复应力作用下,晶粒可能发生滑移、变形或粗化。例如,某批次铍铜弹片经10万次插拔测试后,晶粒尺寸从初始的15μm增长至25μm,导致硬度下降20%,此为疲劳累积的典型表现。
相结构演变:部分铜合金在疲劳过程中可能发生动态再结晶或第二相析出。通过浸蚀剂(如FeCl₃溶液)显示相界面,可评估析出相的分布是否均匀,若局部聚集则易成为应力集中点。
二、金相检测的关键步骤与标准化流程
取样与制样
取样位置:优先选择弹片弯折处或接触点,此处应力集中最显著(图2)。对于已失效弹片,需包含断裂面及相邻区域。
制样工艺:采用树脂冷镶嵌保护边缘,避免热镶嵌导致组织变化。抛光时使用金刚石悬浮液(1μm)至镜面效果,确保无划痕干扰观察。
组织显示与观察
浸蚀剂选择:铜合金常用Kalling's试剂(2g CuCl₂ + 40mL HCl + 40mL乙醇)显示晶界;钢制弹片则采用4%硝酸酒精溶液。
定量分析:结合图像分析软件(如Image-Pro Plus),测量晶粒尺寸、裂纹密度及第二相占比。例如,某案例中弹片的裂纹密度超过5条/mm²即判定为高风险失效。
疲劳等级评定
根据《GB/T 34895-2017 热处理金相检验通则》,摩凯电子制定内部评级标准(表1):
疲劳等级 晶粒变化 裂纹特征 判定结果
1级 无粗化 无可见裂纹 合格
2级 局部粗化≤20% 表面微裂纹≤50μm 预警
3级 整体粗化>20% 内部裂纹>100μm 失效
三、实际案例分析:某型号弹片早期失效的解决方案
背景:某客户反馈弹片在5万次插拔后出现接触不良。
检测过程:
宏观检查:发现弯折处存在肉眼可见的微裂纹。
金相分析:
500倍下观察到晶粒尺寸不均匀,最大达30μm(原始设计≤20μm)。
裂纹沿晶界扩展,并伴随少量氧化物夹杂(图4),表明材料纯净度不足。
改进措施:
优化热处理工艺:将时效温度从320℃调整至300℃,减少晶粒粗化风险。
提升材料纯度:要求供应商将非金属夹杂物等级控制≤1.5级(原为2级)。
效果:改进后弹片通过15万次插拔测试,金相检测显示晶粒均匀性提升40%,无新增裂纹。
四、技术延伸:结合其他检测手段提升精度
显微硬度测试:在弹片不同区域(弯折区/平直区)测量HV值,若硬度波动>10%,提示组织不均匀。
扫描电镜(SEM)分析:对疲劳断口进行形貌观察,区分韧性断裂(韧窝状)与脆性断裂(解理面),辅助判断失效模式。
有限元模拟:通过应力分布模拟,预测高疲劳风险区域,指导金相检测的针对性取样。
五、总结与建议
金相检测是连接器行业质量控制的“显微镜”,需结合材料特性、工艺参数及使用场景综合解读。摩凯电子建议:
定期抽检:对量产弹片按批次进行金相抽检,建立疲劳寿命数据库。
工艺闭环优化:将检测结果反馈至材料选型、冲压成型及热处理环节,形成全流程管控。
标准化培训:检测人员需掌握《GB/T 13298 金相显微组织检验方法》等标准,确保结果一致性38。
通过上述实践,摩凯电子成功将SIM卡座弹片的平均寿命提升至行业标准的1.5倍,为客户提供了更可靠的产品保障。